
by Marnie Werner, research director
Much of the blame for the last winter’s costly delays in rail shipping—“unprecedented,” in the words of State Rep. Frank Hornstein, chair of the House Transportation Committee—was placed on the terrible weather and on the influx of North Dakota oil. Hundreds of Minnesota businesses faced spiraling transportation costs while others were left with millions of dollars of goods on their hands waiting for trains and rail cars to take their products to market, creating costs that in both cases get passed on to consumers.
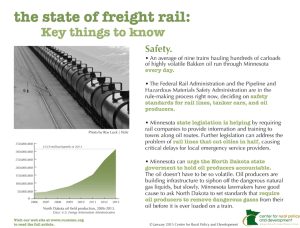
Regardless of the cause, however, what last winter’s gridlock revealed was the extent of the larger problem of robust industry sectors—agriculture, mining, oil, and the coal needed to power these industries—all competing for rail resources that haven’t caught up to the economy’s recovery.
At the same time, rail is also receiving increased attention due to safety issues raised by the millions of gallons of oil rolling through the state since the start of the North Dakota oil boom four years ago.
The rail crisis has eased some since last winter and rail companies have taken steps to improve safety, but both capacity and safety will require long-term fixes. America’s largest railroad companies—Class I railroads—expect demand for shipping tonnage to soar by 45% in the next 25 years, and despite the recent drastic drop in oil prices, oil shipments from North Dakota are not expected to slow down in a meaningful way for at least the next few years.
The largest railroad companies have spent billions of dollars to increase capacity, efficiency, speed, and safety and have pledged to spend billions more, but the upgrades will take years to complete. While rail is a private-sector industry regulated almost entirely by the federal government, the state can and has taken steps to address both capacity and safety issues, but more can be done.
The conversation will need to include private, state, and federal efforts to improve safety and safety training, to coordinate planning with other transportation modes, including barges, pipelines, roads, and bridges, and to assist Minnesota’s smaller rail lines in upgrading their infrastructure to help them continue providing needed services in Greater Minnesota.
Rail’s role in Minnesota’s economy
With nearly 4,500 miles of track, Minnesota’s rail network is more extensive than most states’. Minnesota’s railroads connect to other rail networks across the country, to Canada and Mexico, and to other modes of transportation.
In Greater Minnesota, freight rail moves millions of tons and billions of dollars worth of products every year for farms and businesses, from grain to finished food products to taconite, fertilizer, forest products, and manufactured goods. (Map of freight rail.) In the Twin Cities, which is a major interchange on the national rail network, goods may stop there or they may be transferred to other rail lines or other modes of transportation, sending Minnesota-made products out to all parts of the country and the globe.

In 2013, the Minnesota departments of Transportation and Employment and Economic Development released the Freight Rail Economic Development report, a study mandated by the 2012 Legislature to explore ways to expand rail-related business in the state.[1] Some of the findings from the report state that:
- Minnesota’s gross domestic product was one of the top five fastest growing in the United States in 2013. A growing economy needs a transportation network that can get products from producer to consumer.
- Minnesota has a diverse economy, a significant portion of which involves moving large volumes of bulk commodities long distances, a situation well suited for rail.
- Few states have the kind of rail connections Minnesota has, which promotes both domestic and global trade.[2]
- Using rail reduces truck traffic on rural and metro roads, saving on the cost of repair and maintenance and reducing congestion. The report estimated that the state saved $33 million in road repair costs in 2011 due to the amount of goods shipped by rail instead of by road.[3]
Rail can be thought of as an infrastructure similar to highways and municipal water systems. Unlike these publicly funded infrastructures, however, freight rail is a private industry and operates as a private business (as opposed to passenger rail, which is publicly funded). The federal Surface Transportation Board classifies railroads by their size based on annual revenue. Class I railroads make more than $379 million a year; Class IIs, $30 million to $379 million; and Class IIIs, less than $30 million.[4] Four Class I railroads, one Class II, and 17 Class IIIs operate in Minnesota.
The four Class I railroads operating in Minnesota are all familiar names: Burlington Northern Santa Fe (BNSF); Union Pacific (UP); plus two Canadian companies, Canadian Pacific (CP) and Canadian National (CN).
Rail moves about 40% of the nation’s goods. In 2012, Class I railroads moved 19.7 billion tons of goods throughout the U.S., according to the Association of American Railroads. The organization is projecting demand for freight transportation to rise to 28.5 billion tons by 2040.[6] Class I freight rail is regulated almost completely at the federal level. Therefore, the state has little influence regarding Class I rail companies compared to infrastructure like the highway system.
How the rail industry got to where it is today
Minnesota and the United States had a robust network of freight and passenger rail companies up into the 1950s. However, as the interstate highway system developed, encouraging more shipping via truck, and as more families bought cars, business began dropping off for both freight and passenger rail. Rail companies were also regulated tightly by the federal government as to what services they needed to provide, what routes needed to be maintained whether they were profitable or not, and how much they could charge.
By 1980, many of the nation’s 40-some large rail companies were headed for or already in bankruptcy. That year, Congress passed the Staggers Rail Act, deregulating the rail industry. Besides lifting price controls, rail companies were now allowed to abandon unprofitable lines and to merge and consolidate.
Today there are only seven large American rail companies left,[7] including BNSF and UP.
Where rail is headed now
Since the Staggers Act removed controls on the rail industry, the goal of rail companies has been improved efficiency. Moving more cars to move more goods at the same time, along with faster loading and unloading of rail cars means a faster turnaround time for those cars to carry another shipment elsewhere.
One of the biggest advancements in efficiency over the years has been the introduction of the “unit” or “shuttle” train. Years ago, trains of various lengths rumbled by pulling cars carrying a variety of products, from grain to coal to automobiles and shipping containers. The individual cars were picked up at different locations along the way and dropped off in the same way. Today we often see unit or shuttle trains, sets of 75 to 110 cars all carrying a single product (for example, grain or oil) and loaded or unloaded at a single facility. Handling a large amount of a single commodity in this way increases the speed of loading and unloading and decreases travel time, since all cars are heading to the same location. These trains, often more than a mile long, require specialized shuttle terminals that can accommodate the train’s length and can load and unload the product within a specified amount of time.
To further increase efficiency, rail companies are also moving toward larger rail cars and locomotives that can pull heavier loads. The weight of covered hopper cars for transporting grain, for example, has increased from 263,000 pounds (the weight of the car loaded) to 286,000 pounds. Some rail carriers are considering weights of 315,000 pounds. While increasing efficiency, this heavier equipment will also require upgraded, sturdier rails, rail beds, and bridges to support the increased weight.
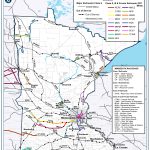
Short line rail
All this emphasis on faster times and greater efficiency, however, means that Class I rail companies are less willing to take on small shipments. After deregulation in the 1980s and 1990s, Class I rail companies were allowed to abandon unprofitable lines, usually lines that passed by fewer, smaller customers. Many of those customers still needed shipping options, however, and therefore over the years smaller railroad operators purchased the lines and now handle volumes that would be unattractive to Class I rail lines.
Short line operations run from large to small and may handle very specific jobs. Minnesota Southern, a short line operating in the very far southwestern corner of the state, picks up shipments along its line and carries them to the connection with BNSF at Manley, Minn., near the South Dakota border or to the UP line at Agate, Minn., just southwest of Worthington. Northern Plains Railroad, operating in northwestern Minnesota and northeastern North Dakota, offers services such as transloading (loading goods from the train to a truck or vice versa), storage, track repair and maintenance, rail car repair, and locomotive repair. The former Duluth, Missabe & Iron Range Railroad, now a part of Canadian National, hauls taconite from Iron Range mines to the ports in Duluth, Two Harbors, and Superior.
Twin Cities & Western illustrates the relationship between Class I and Class III lines and their impact on Minnesota’s economy. TC&W is the largest of the Class III lines in Minnesota. Operating a 229-mile line through some of the nation’s most productive farmland from Milbank, S.D., to the Twin Cities, TC&W handles approximately $1.5 billion in client goods each year, according to the company. In recent years, the rail company has handled goods going to and coming from 39 U.S. states, seven Canadian provinces, and several states in Mexico, said Dave Long, vice president of marketing and sales for TC&W.
TC&W is able to carry goods from such a wide area because it connects with all four Class I rail lines in St. Paul. At these intersections, short lines drop off small shipments that are then aggregated with other small shipments to make a shipment large enough to be cost-effective for a Class I line to deliver over a long distance.
But while short lines have the potential to offer valuable transportation options for Minnesota producers, many of them are woefully under-capitalized. They make enough to operate and maintain their tracks, but not enough to re-invest in upgrades, said Dave Christianson, project manager for MnDOT’s Statewide Rail Plan.
What happened last winter: Too much demand, not enough supply
The core of the problem last winter was that there was too much demand vying for the amount of infrastructure available, and the severity of last winter only brought this problem painfully into focus. The market pressures that contributed to last winter’s shipping woes:
- Economic growth. Minnesota’s economy has been very productive. When the economy came back after the recession, it came back with a bang and in different places, both industry-wise and geographically, putting serious pressure on an infrastructure that, like any other, cannot expand at lightning speed to meet the current need.
- New markets for grain. The markets for Minnesota grain have shifted from Europe to Asia. Until a few years ago, Europe was a larger market for Minnesota grain, which shipped east via Duluth and the Great Lakes. A large percentage of farm products are now being sent by rail to ports on the West Coast. From there they are shipped to Asia, especially China. Sending the grain west, however, puts it on the same tracks as North Dakota oil heading east into Minnesota.
- High demand for coal. Besides grain, rail companies are shipping record amounts of coal to Minnesota power plants for electricity, according to BNSF representative Brian Sweeney.[10]
- Interruption in propane supply line. A pipeline that had been sending propane from Canada to Minnesota was reversed in early 2014, sending supply north and cutting off 40% of Minnesota’s propane supply. Propane is used not just for heating and cooking in rural areas, but a large amount is also used for drying grain before being shipped to market. Propane suppliers have been making up for the transportation shortfall by leasing more rail tankers and converting their facilities to accept fuel by rail.[11]
- Shipments of Bakken oil on Class I lines zoomed from 9,500 carloads in 2008 to over 400,000 carloads in 2013.[12] “Did anyone anticipate oil?” asks John Apitz, who represents the Minnesota Regional Railroad Association. “The railroads didn’t.” A large amount of Bakken oil goes to East Coast refineries, which are not served by pipelines.
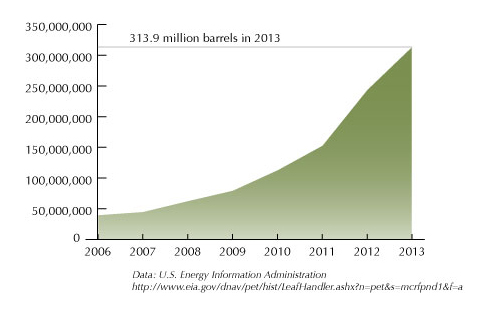
The solution isn’t as simple as adding more engines or more cars, says Apitz. Federal regulations limit how many trains can be on the tracks at any one time, because the spacing and timing of trains is crucial for safety, especially along single-track lines.
Current challenges
To address the current capacity problem, railroads are building out their track and facility infrastructure. According to Amy McBeth, BNSF’s director of public affairs for the Upper Midwest, the company estimates it will have spent $5.5 billion in 2014, including $120 million in Minnesota, and is budgeting another $6 billion in 2015. (Read BNSF’s press release.)[13] BNSF is using the funds to increase and improve track capacity, including double-tracking single-track lines, to expand facilities for storing and transferring goods, and to hire an additional 3,000 employees.[14]
The railroad company has pledged to double-track single-track lines along the Bakken route, including points in Minnesota that have proved troublesome, BNSF’s Brian Sweeney told legislators during a Sept. 30 meeting of several legislative committees called to address the rail issue. Double-tracking is a crucial part of increasing capacity as well as safety. For example, when maintenance takes place on a single track, all traffic must be stopped in both directions. Completing double tracking in Minnesota, however, will take at least three years, Sweeney said.
Long-term challenges
Cost of transport
As the law of supply and demand decrees, the more demand there is for an item, the higher its price will go. For that reason, shippers will be left with high transport costs for a while as railroads work to build out their infrastructure to meet the demand.
A fundamental cost to the shipper is the cost of a rail car. While the railroad companies and shippers own some rail cars themselves, most are owned and leased out by third-party companies such as GATX, which auction off lease contracts of individual rail cars and sets of rail cars. The winning bidder can then use the cars or turn around and lease them out again to someone else (at a higher price if they intend to make a profit).
When there is high demand for rail cars, leases can change hands several times before any goods are ever placed in the car. As a result, rail car prices can spiral upward. When there is low demand, the price drops. Demand often rises and drops seasonally. It has been low at the end of 2014 in large part because of relatively low grain prices, says Dave Long with Twin Cities & Western. Farmers are choosing to store their crops right now and wait for crop prices to recover.
Transport costs are a top concern to producers of any industry since they are part of the production cost and cut into profits. These costs are more of an issue in agriculture, however, because unlike most industries, ag producers have no way of passing the cost on.
“The world isn’t going to pay any more for that grain just because freight costs more,” said University of Minnesota professor and grain marketing economist Ed Usset in a November 2014 Star Tribune article.[15] “The price [farmers receive] gets pushed down, not pushed up.”
Paul Mattson, grain department manager at West-Con, a large grain-handling cooperative in western Minnesota, said they didn’t have any trouble with delays last winter. That, he said, was because they planned ahead, but they also took a deep breath and paid the full market rate for their rail cars even though the prices affected their competitiveness. They also turned more to trucking as the cost of rail rose.
West-Con officials have also decided, though, to make constructing a new terminal in Appleton part of their long-term plan. Currently the co-op operates two terminals, one in Holloway, Minn., and one in Milbank, S.D., both on the BNSF line. A new terminal in Appleton would be on the Twin Cities & Western line. TC&W’s connections with all four Class I lines give West-Con more shipping options, Mattson said.
Shippers have preferred rail because it has tended to be less expensive than shipping by truck, especially for large amounts of bulk goods and commodities over long distances. As the price of rail rises, however, other modes start to look more attractive. For that reason, some shippers are turning to barges again, sending grain and other goods down the Mississippi rather than to the West Coast. “With rail service being what it is, [shippers are] willing to drive further to access the river,” said Mike Steenhoek, executive director of the Soy Transportation Coalition, an Iowa-based coalition made up of 12 state soybean boards, including Minnesota, and two national soybean groups. [16]
Costly delays
Even with the low price of grain in the fall and winter of 2014, there is still a great deal of congestion on the rail lines, says Bob Zelenka, executive director of the Minnesota Grain and Feed Association. When a shipper has contracts with customers and is ready to ship, delays in moving product can be very costly. Elevators lost hundreds of thousands of dollars in contracts last winter because they were unable to move grain in time to the West Coast, Zelenka said. Ships leave port on a pre-determined schedule and cannot wait for a delayed trainload of grain. Now a labor dispute at West Coast ports is rippling back into the Midwest economy. A recent article in the Minneapolis Star Tribune on West Coast port labor troubles provides a good primer on the economic impact of shipping slow-downs for Minnesota goods. [17]
Unfortunately, the rail lines to the West Coast run right through the North Dakota oil fields. Were the delays of last winter the fault of North Dakota oil? It depends on who you ask. Shippers of products maintain oil shipments were given priority over everything else, if for no other reason than oil companies could afford to lease cars at any price. Rail companies insist they do not give priority to oil and that oil shipments were just as delayed as everything else. BNSF’s Brian Sweeney told legislators that oil shipments were delayed 24% of the time last winter compared to grain being delayed 22% of the time.
One thing is sure, though: North Dakota oil’s sudden arrival only added to the competition for space on the rails. The surge in oil production and shipping from the Bakken fields in North Dakota hit so fast that oil wasn’t even mentioned in the state’s current freight rail plan, which was written five years ago. It promises to be a central topic in the 2015 update.
The ripple effect of bigger and better equipment
The oil train controversy, however, is masking another very real problem for towns across the state. In Greater Minnesota and in the Twin Cities, places like Benson and Coon Rapids are finding their cities cut in half when very long unit trains park in the middle of town waiting for their turn to move forward. The situation is not just an inconvenience to drivers, but a roadblock for emergency service providers, who lose precious extra minutes when they find their main routes cut off by a parked train. Gov. Dayton met with state, local and rail officials Dec. 22 in Coon Rapids to discuss the problem. Upwards of 100 trains pass through that city every day, according to that city’s fire chief, John Piper.[18]
At the same time, the new standards being adopted by the Class I railroads for heavier cars and longer trains are making it difficult for short lines to interchange with them because of the need for tracks and bridges that can handle the added weight. Short lines provide needed transportation services, but their rail network is not very robust, says MnDOT’s Dave Christianson. Several lines are in serious need of repair, he said.
“This is a concern for short lines already operating with marginal track and bridge structures and 10-mile-per-hour speed limits,” Matthew Pahs, a former MnDOT planner, wrote in an article on rail for the Rural Minnesota Journal all the way back in 2009.[19]
The problem is that short lines generally don’t have enough capital to make meaningful improvements to their lines. MnDOT operates the Minnesota Rail Services Improvement loan program (MRSI), established nearly forty years ago to assist railroad companies and shippers in improving their facilities and rail lines by offering interest-free loans. Loans are capped at $200,000 each, however, which is insufficient for most improvement projects today, says Christianson. According to the Minnesota Grain and Feed Association’s Bob Zelenka, a complete grain terminal built to handle 110-car shuttle trains can cost upwards of $30 million.
The program was very useful in the 1980s and 1990s, said MRRA’s John Apitz, and many small elevators used MRSI loans to make improvements. However, today money is too cheap and an MRSI loan involves too much paperwork for the amount received, he said.
Safety
The significant priority today, though, is safety, and for the past two years the issue has focused squarely on oil. In 2014 at least nine trains hauled hundreds of tanker cars filled with oil from the Bakken range in North Dakota across Minnesota, according to MnDOT.[20]
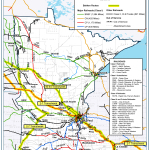
Bakken crude oil is highly flammable and dangerous. For an excellent review of the issues that come with moving crude oil by train, read MnDOT’s Highway-Rail Grade Crossings report. The oil, which has been at the root of at least five explosive rail accidents over the last two years,[21] is so flammable because of the naturally occurring natural gas liquids, or NGLs, dissolved in the crude oil, such as butane, ethane, and propane. The oil was deemed so dangerous, in fact, that the Federal Rail Administration and the Pipeline and Hazardous Material Safety Administration issued emergency orders classifying the oil under the most dangerous and highly controlled category of flammable liquids and requiring strict labeling standards.[22]
The scenario everyone fears is, of course, a derailment like the one that happened in Lac-Megantic, Quebec, in July 2013, when a runaway train carrying Bakken crude derailed and exploded in the middle of the town of 5,900, killing 47 people and devastating a good part of the downtown. Several legislators at the Sept. 30 hearing in St. Paul made it clear that they were concerned about the number of oil trains seen sitting on sidings in towns along the BNSF line from Fargo to St. Paul. New federal policies are currently being developed to set safety standards for rail carriers, including standards for new reinforced tanker cars and lower speed limits, but the process could take another one to two years, according to MnDOT.[23]
Railroad companies are responsible for the upkeep and safety of their tracks and equipment, and BNSF, which carries 75 percent of the North Dakota oil moving through Minnesota, is working on the situation, Sweeney told legislators. Investment priorities include track upgrades, double-tracking, and acquiring new, reinforced tanker cars. Orders for these new cars are backlogged two years as they overwhelm manufacturers, however, an MPR article from last spring stated.[24]
The state is taking measures, however. Legislation passed during the 2014 session addresses a number of safety issues. Among them:
- Requiring a $2.5 million annual assessment through 2017 on rail companies and pipeline companies operating in Minnesota. This assessment will go to pay for firefighter training and other safety preparedness needs in communities along routes carrying hazardous materials.[25]
- Funding was approved to increase the number of state rail inspectors from one to four, plus a hazardous materials inspector. Those inspectors were hired over the summer.[26]
- Railroad companies must offer training in handling oil and hazardous substance emergencies to fire departments in communities along their routes and offer refresher training at least once every three years.[27]
- Railroad companies must communicate with local government emergency managers and fire departments along their routes at least annually to coordinate emergency response plans.[28]
- In the event of an incident, railroads must provide a qualified person to respond to the local emergency response team within one hour by phone and must have qualified personnel at the site of the incident within three hours.[29]
BNSF points out that it is already providing training. According to BNSF’s Amy McBeth, BNSF trained 1,200 first responders in 200 sessions across the state in 2014, while another 130 Minnesota firefighters attended special crude-by-rail safety training at a BNSF facility in Pueblo, Colo.
Responsibility for the safety of oil trains doesn’t fall completely on the rail companies, however. Technology exists that allows oil companies to siphon off the highly flammable gases from the crude oil before it ever goes into the tank cars.[30] Texas oil fields have had the infrastructure in place for years to do this and producers in fact sell those gases as part of that state’s large Gulf Coast petrochemical industry. This infrastructure doesn’t exist in the North Dakota oil fields yet. The federal government could set policy to require all oil fields to use this practice, called “stabilizing,” but has chosen not to do so, leaving the decision to the individual states.[31] North Dakota has so far chosen not to use stabilization, instead going with a practice called “conditioning,” which an article in Railway Age magazine[32] argues is far less effective. An alternative to stabilization and conditioning is flaring, or simply burning off the gases, which brings with it its own set of environmental detractors. Regardless of the solution, however, the security of the thousands of oil tankers passing through populated areas across Minnesota on their way to East Coast oil refineries is paramount to both Greater Minnesota and the Twin Cities.
Recommendations
The rail industry functions as a private business and is largely regulated by the federal government. However, there are areas where state legislators can have an impact.
Ensure that freight rail is included in any coordinated transportation and economic development planning. Transportation is more than highways. Freight rail is a multi-state infrastructure that can benefit the economies of all the states it passes through. Policy makers should not underestimate the economic impact freight rail has and the access it gives Minnesota’s businesses to markets around the world. Proper planning to coordinate the development and interconnection of freight rail, highways, pipelines, and river traffic will improve the efficiency of the finished projects, ideally lowering costs on the back end for shippers. MnDOT’s Statewide Rail Plan and Statewide Freight System Plan coordinate freight rail into the state’s other transportation plans.[33] The Freight Rail Economic Development plan report provides many examples of how to include freight rail in economic development planning.
In particular, transportation policy makers must decide where short lines fit in. The ongoing changeover to heavier rail cars by Class I railroads presents a definite hurdle for these smaller lines that provide vital services to rural Minnesota’s economy.
Minnesota Rail Service Improvement program. Everyone to a person, when asked how the state could help improve rail access for Minnesota businesses, said improve the Minnesota Rail Services Improvement program. The MRSI program can be still quite relevant to Minnesota’s Class III companies, which need access to inexpensive funds for capital improvements to their rails and bridges if they are to remain competitive. The program is also open to shippers to help them upgrade their facilities. Critics say the loan caps are too low and the paperwork, administration, and regulations surrounding the program too onerous to make the loans worth it.
Safety. The achievements in rail safety approved by the state legislature in the 2014 session show great promise. Suggested further measures could include:
Addressing the issue of rail lines that cut cities in half. Long trains, whether they carry oil or not, present a big problem when they park across the middle of a city, causing critical delays for local emergency service providers.
Calling on the Federal Rail Administration and the Pipeline and Hazardous Materials Safety Administration to move past proposing new safety standards for rail lines, tanker cars, and oil producers and actually approve them. The sooner these agencies can adopt standards, the better.
Urge North Dakota’s state government to set real safety standards. Given the thousands of oil tankers moving through the state every month, Minnesota has good cause to urge North Dakota’s state government to set standards that require oil producers to remove dangerous liquid gases from their oil before it is ever loaded on a train.
[1] Minnesota Department of Transportation, Freight Rail Economic Development, 2013.
[4] U.S. Department of Transportation, Surface Transportation Board, FAQs.
[5] MnDOT, Railroad Companies Serving Minnesota.
[6] Association of American Railroads, Freight Railroad and Capacity Investment, April 2014.
[7] U.S. Department of Transportation, Surface Transportation Board, FAQs, Economic and Industry Information.
[10] Minnesota House of Representatives, Public Information Services, audio recording of Transportation Finance Committee hearing on rail held Sept. 30, 2014.
[11] MN House of Representatives, audio recording of Transportation Finance Committee hearing on rail, Sept. 30, 2014; Andy Shaffer, “Propane industry scrambles to replace supply from major pipeline,” Minneapolis Star Tribune, Dec. 7, 2013; Kevin Yanik, “Cochin reversal project creates pipeline pressures,” LP Gas Magazine, Oct. 30, 2013.
[12] Association of American Railroads, “Moving Crude Oil by Rail,” Sept. 2014.
[13] Burlington Northern Santa Fe news release Nov. 20, 2014.
[14] MN House of Representatives, audio recording of Transportation Finance Committee hearing on rail, Sept. 30, 2014
[15] Tom Meersman, “Rail congestion sends more grain to market on river barges,” Minneapolis Star Tribune, Nov. 16, 2014. A good introduction to the dilemma of transportation costs for farmers.
[16] Tom Meersman, “Rail congestion send more grain to market on river barges,” Minneapolis Star Tribune, Nov. 16, 2014.
[17] Tom Meersman and Kavita Kumar, “Shipping slowdown ripples into the Midwest,” Minneapolis Star Tribune, Dec. 5, 2014.
[18] KSTP news, “Train traffic creates safety concerns in Coon Rapids,” Dec. 22.
[19] Matthew Pahs, “Expanding the Effective Use of the Rail System in Rural Minnesota,” Rural Minnesota Journal, 2009.
[20] MnDOT, “Improvements to Highway-Rail Grad Crossings and Rail Safety,” December 2014.
[21] Lac Megantic, Quebec, in July 2013; Aliceville, Ala. November 2013; Casselton, N.D., December 2013; New Brunswick, January 2014; Lynchburg, Va., April 2014.
[22] MnDOT, “Improvements to Highway-Rail Grade Crossings and Rail Safety,” December 2014.
[23] MnDOT, “Crude-by-rail transportation and safety in Minnesota.”
[24] Dan Gunderson, “Volatile Bakken oil, aging tank cars raise the stakes for Minnesota rail safety,” Minnesota Public Radio, March 12, 2014.
[25] MnDOT news release, July 1, 2014; Minnesota Office of the Revisor of Statutes, 2014 Statutes, Article 299A. 55.
[26]Minnesota Office of the Revisor of Statutes, 2014 Statutes, 219.015.
[27]Minnesota Office of the Revisor of Statutes, 2014 Statutes, 115E.042.
[28]Minnesota Office of the Revisor of Statutes, 2014 Statutes, 115E.042.
[29] Minnesota Office of the Revisor of Statutes, 2014 Statutes, 115E.042.
[30] Kristen Hays, “Safety debate eyes taming Bakken crude before it hits rails,” Reuters, May 12, 2014.
[31] David Thomas, “Federal hazmat regulator AWOL from North Dakota oilfields,” Railway Age, Sept. 26, 2014.
[32] David Thomas, “Federal hazmat regulator AWOL from North Dakota oilfields,” Railway Age, Sept. 26, 2014.
[33] MnDOT, “Freight Rail Planning and Development in Minnesota.”